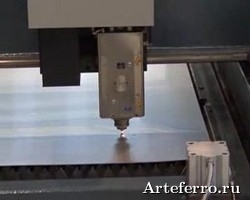
Среди большого количества способов обработки металлопродукции, лазерная резка металла занимает лидирующие позиции. Связано это с тем, что после традиционных методов резки обычно требуется дополнительная обработка кромок, вызывают недоверие также качество и точность реза. Лазерная резка позволяет добиться любой конфигурации разрезаемого материала, а это может быть, как нержавеющая сталь, так и другие материалы, среди которых медь, алюминий и латунь.
Технология процесса
В отличие от механических способов резки металла, таких как штамповка и рубка на гильотинных ножницах, в случае с лазерной резкой используется сконцентрированный световой луч, имеющий высокую мощность, что позволяет выполнять работы по раскрою и сверлению материалов различной толщины и прочности. Процесс можно разделить несколько этапов:
- нагрев;
- плавление;
- испарение;
- удаление из зоны реза расплавленного металла.
Сфокусированный луч, направленный к месту реза, сначала нагревает металл, затем начинается его плавление и резка. После этого происходит испарение и удаление расплавленного материала, для чего используется вспомогательный газ. Используемые для этой цели кислород и азот позволяют увеличить скорость резки, открывая новые возможности, связанные с увеличением толщины разрезаемого металлопроката.
Преимущества и недостатки
Каждая технологическая операция имеет, как свои преимущества, так и недостатки. Если сравнивать лазерную резку металла с другими методами, преимущества этого метода являются очевидными, и в их числе можно отметить следующие:
- Края заготовки не деформируются и не требуют дополнительной зачистки, что свидетельствует о высоком качестве реза.
- Отсутствует механическое воздействие на металл, что не ухудшает его свойства.
- Есть возможность изготовления деталей сложной конфигурации, включая возможность резки труб и сложных профилей.
- Высокая производительность.
- Экономичность.
Среди большого количества преимуществ именно экономичность привлекает чаще всего. Стоит отметить, что лазерный раскрой позволяет значительно сэкономить используемый металл, что происходит за счёт сокращения ширины реза, которая лежит в пределах 0,07-0,1 мм. Несмотря на все преимущества, есть у резки лазером и незначительные недостатки. Среди них можно выделить небольшое, но ограничение по толщине разрезаемого металла. Таким способом можно разрезать углеродистую, нержавеющую сталь и алюминий толщиной от 0,2 до 20 мм, максимальна толщина медной заготовки при этом, составляет 15 мм, а изделий из латуни – 12 мм. Кроме этого можно отметить сравнительно низкую скорость резки, что вполне покрывается качеством.
Таким образом, даже поверхностное ознакомление с процессом, позволяет сделать выводы о том, что лазерная резка металлов на настоящий момент не имеет конкурентов. Даже не смотря на некоторые недостатки, лазер сегодня является незаменимым в машиностроении и других отраслях промышленности.
По материалам сайта metalproces.ru.